La gran parte delle scarpe da montagna impermeabili prevede l’uso della membrana come fodera sagomata a ‘calzino’ (il cosiddetto ‘bootie’ o ‘fodera impermeabile’) che viene inserita nella scarpa restando però comunque separata dalla tomaia e con uno spazio nel mezzo.
Il sitema “bootie” è semplice ed economico da produrre, ma presenta numerosi svantaggi. Il più grave di questi è che l’acqua (pioggia, neve o ambiente umido) non viene arrestata sullo strato esterno (la tomaia) ma può facilmente penetrare fino alla fodera impermeabile e ristagnare nello spazio tra questa e la tomaia: il piede resta sì asciutto ma l’acqua penetrata appesantisce la scarpa, e riduce la traspirabilità e l’isolamento termico.
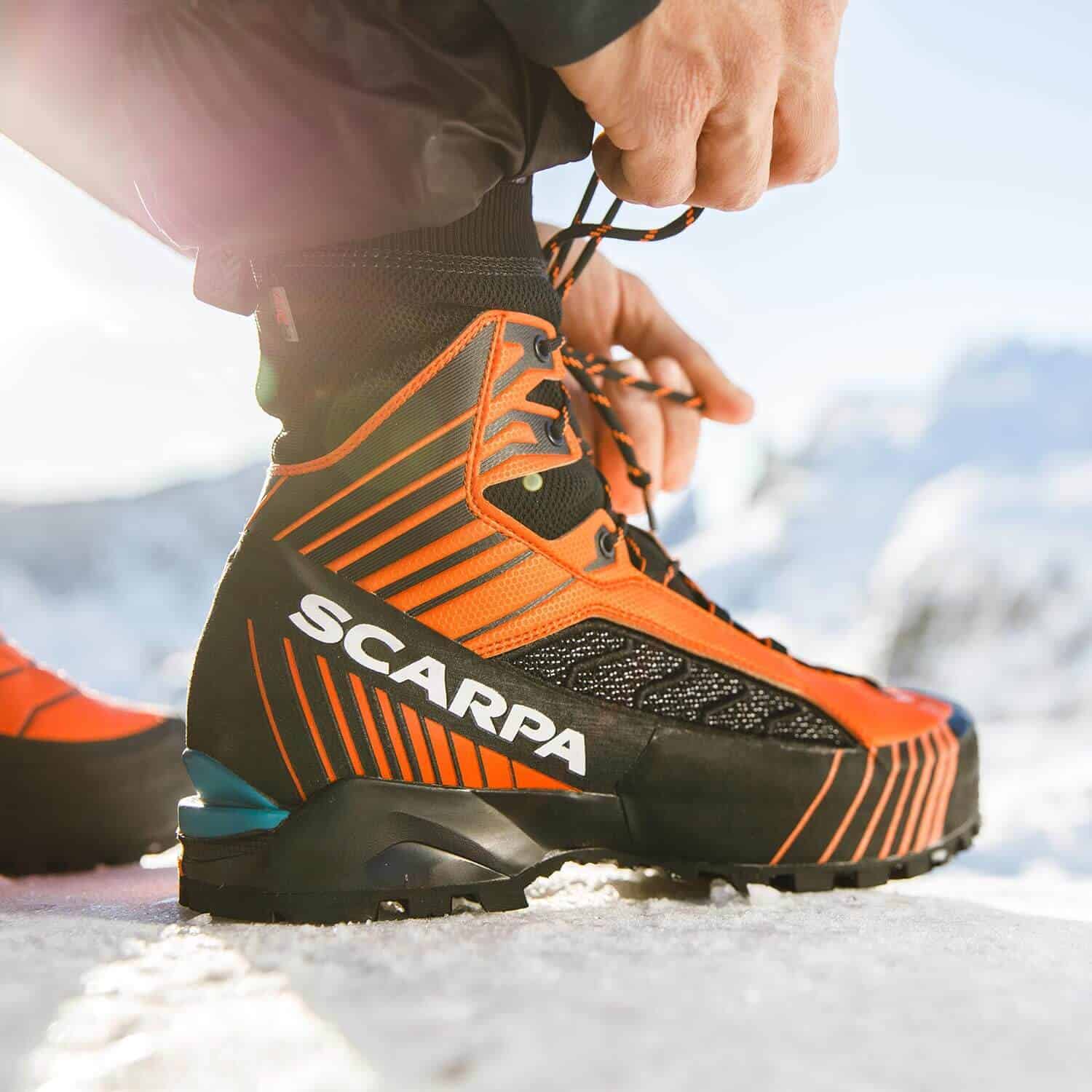
Con HDry la membrana viene invece laminata direttamente sulla superficie interna della tomaia già cucita in una conformazione 3D, completa di ganci e occhielli. Tramite la macchina di laminazione brevettata HDry, la membrana impermeabile viene saldamente unita, con dei micropunti di colla, alla tomaia. In questo modo il materiale di tomaia (pelle o tessuto), le cuciture e ogni altro potenziale punto di ingresso vengono sigillate. Ciò garantisce che l’acqua venga bloccata allo strato più esterno della scarpa, che resta così leggera e asciutta in ogni condizioni atmosferica.
È importante notare che l’innovazione di HDry non risiede nella membrana, ma piuttosto nel modo in cui la scarpa è costruita, in particolare nel processo di laminazione della membrana alla tomaia. La membrana può quindi essere scelta in base al tipo di utilizzo finale, utilizzando criteri quali performance, efficienza e, soprattutto, sostenibilità: la membrana HDry è infatti PTFE-free, PFC-free ed è certificata OEKO-TEX Standard 100.
